Business improvement is always at the heart of any successful business. In 1913, Henry Ford invented the moving assembly line which helped him produce more cars in less time. Because of this, they were able to reduce the production cost, deliver more cars on time, and improve the overall efficiency.
In 1950, Taichi Ohno of Toyota developed lean production which helped develop revolutionary product development and production process.
In 1986, Bill Smith of Motorola developed the six sigma methodology that helped organizations measure the quality of their products. In 2003, they took this effort further and rebranded their efforts as Digital six sigma.
Fast forward to today, the world is filled with digital, software, and manufacturing companies and their competition is increasing with each passing second. To sustain in this competitive world, they have to focus on the business improvement process and make their organization better in order to stand out.
Today business process improvement is the term often used by organizations who are looking to optimize existing processes and build new ones.
The term is often interchangeably used with continuous improvement process, business process optimization, and business process automation. All these terms are similar and may vary slightly based on the requirement of the organization.
In this blog post, we will help you understand:
- What is Business Process Improvement?
- Difference between BPM and BPI
- When are your Business Processes at risk?
- What are the benefits of Business Process Improvement?
- Different Business Process Improvement Methodologies
- Business Process Improvement steps
What is Business Process Improvement?
Business Process Improvement (BPI) is a management practice that uses different methodologies to identify areas where organizations can improve accuracy by mapping, analyzing, redesigning, implementing, reviewing, and refining.
The ultimate aim of BPI is to reduce process completion time, eliminate resistance, ensure smooth processes, and follow regulatory compliance to improve the efficiency of the organization by making the most of available resources.
Businesses are focusing on creating business rules and following compliance laws to achieve desired business outcomes.
BPI helps address the root cause and improve processes but people often tend to confuse BPI with BPM(Business process management). So, before diving deep into the topic, let’s understand the difference.
Difference Between BPM and BPI
Over the years, business process management(BPM) has evolved into a holistic management discipline. The focus of BPM is to align all organizational efforts with individual processes and resources to drive strategically defined business goals. With BPM, a company can manage the whole process matrix within the organization.
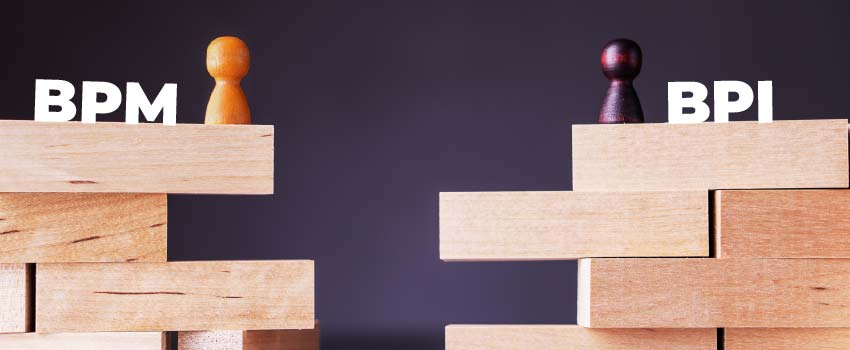
On the other hand, BPI is focused on improving specific processes. BPI is a subset of BPM and its scope is limited to processes.
BPM is an umbrella term that includes BPI, BPA(Business process automation), and BPO (Business process optimization).
You can’t improve what you are not managing and you can’t manage what you are not measuring. In that sense, BPI provides the base for BPM as it helps organizations focus on key process metrics that could be crucial for the overall business.
Relevant Read: Top 6 business process management challenges
When Are Your Business Processes Under Risk?
Organizations are heavily focusing on business processes but after the implementation of any business process, if it is not measured, tracked, and managed, then the chances of failure are very high.
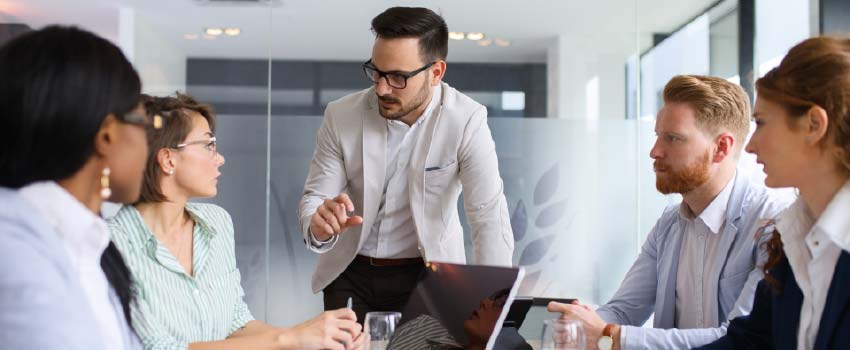
In 2016, a survey was conducted to check the process maturity of organizations and it was found that only 4% of the companies measured and managed all their documented processes.
This is a severe problem and when an organization implements Business Process Improvement, it is necessary to have a strategy in place to regularly measure and manage the deployed processes.
“What gets measured, gets managed.”
– Peter Drucker
If they are not measured, your business process can be at risk. Business processes are complex and managing them at the 11th hour is pointless.
So, it is important to know when your business process is at risk and when to look out for the warning signs. Some examples of such situations are:
- Improper or inadequate knowledge about the business
- Error in business outcomes due to discrepancies in processes
- Delay in communication and time to action
- Process duplication and inaccuracy in processes
The objective of Business Process Improvement is not just to ensure efficiency but also to be proactive and reduce risk.
What are the Benefits of Business Process Improvement?
Businesses are always subject to continuous improvement. Doing so will not only help achieve quality but also enable the organization to stay ahead of the competition.

Here are some organizational benefits of business process improvement:
Quicker time to completion: If the organization is focused on continuously improving existing processes by finding gaps, they can remove unnecessary delays and buffer periods from the process. The optimized version helps them realize value faster.
Efficient processes: Any growing business should continuously look for ways to improve its process. Most people think that only outdated processes need to be addressed but regular improvement keeps your organization up to date and could pave the way for innovation. A last-minute shift to new processes only enables basic functionalities but regular improvement of those processes can help the organization create strides in their respective industries. It also makes the life of the employees much easier as they can adapt to new processes easily if the rollout happens in bite-sized chunks with regular intervals of time.
Incredible experience: Customer experience is usually at the core of any business that wants to succeed. BPI ensures ease of use in your business process which satisfies the needs of customers and encourages them to stay with your product or service longer. Employee satisfaction is also crucial and with BPI, the organization empowers its employees to be efficient and successfully accomplish their tasks. It enhances the overall employee satisfaction as they don’t feel demotivated as they might with outdated business processes.
Improve output: With optimized processes, the company achieves efficiency, allowing them to be consistent with its product or service. It helps them improve quality without investing anything extra in their resources. As a result, organizations retain more customers and improve their bottom line.
Different Business Process Improvement Methodologies
a. Six Sigma
Six Sigma is a BPI process in which the production is 99.99966% defect-free and it is closely associated with statistical modeling and manufacturing. The sigma rating defines the percentage of fault-free products.

This framework was created in 1986 by Mikel Harry and Bill Smith at Motorola. It consists of two methods DMAIC and DMADV. It eliminates business errors and ensures that the processes meet the customer’s expectations. The aim is to improve profitability by measuring the financial impact.
From the perspective of Business Process Improvement, DMAIC is the preferred method as it deals with improvement while DMADV is used to implement new business processes.
DMAIC stands for Define, Measure, Analyze, Improve, and Control. It is a problem-solving model that helps improve and optimize existing business processes. It consists of 5 steps:
- Define: In this phase, you define problems and project goals. It is necessary to set the right expectation up front for better results.
- Measure: Define crucial business points and collect relevant data.
- Analyze: Examine the collected data and identify the gaps and defects in the current process.
- Improve: Enhance existing processes by creating a strategy to overcome the gaps that you analyzed in the previous step.
- Control: After the implementation of the process, control the environment to find out if there are any issues and regularly monitor for sustainable improvement and long-term success.
b. Lean Methodology
The lean methodology was created by Toyota Production System in the 1950s. It changed the way physical goods were manufactured. Today, it has a strong influence over how a business operates across different industries by helping them eliminate waste, improve processes, and boost innovation.

Lean has three main categories:
- Muri: It is a Japanese term that signifies overburdening. In the business world, it can be associated with overburdening the employees, machines, and infrastructure.
- Mura: It refers to the unevenness and inconsistency in processes. Mura is considered to be the cause of Muri and Muda. Mura can be avoided by creating transparent processes especially in functions like supply chain and product design.
- Muda: It means waste. Muda means creating waste during a process that hinders businesses from creating something of quality and value.
When companies use the lean methodology to eliminate the Muri, Mura, and Muda, they progress towards creating a perfect process that aligns with the organization’s vision and achieving their business goals with minimum hiccups.
c. Kaizen Methodology
Kaizen is a Japanese term that means ‘continuous improvement’. It focuses on continuous improvement within an organization. The focus is to constantly make small positive changes that can result in significant organizational growth.

It is considered to be a part of the culture more than a methodology and it seamlessly complements Lean methodology.
“The message of the Kaizen strategy is that not a day should go by without some kind of improvement being made somewhere in the company.”
– Masaaki Imai
It has the potential to improve several business processes and functions across the organization. From marketing to the supply chain, every business process can be improved.
Kaizen finds its roots in World War II when an engineer named W.Edward Deming quickly converted a car factory into a tank factory by finding ways to make changes to minor processes.
This led to a significant change and helped them achieve their objective in record time.
Then Deming went to Japan and helped manufacturers optimize production and scale their business. Lean methodology is derived from Kaizen and helped many industries produce world-class results.
Kaizen satisfies the following three needs of employees:
- Connection: A feeling of camaraderie and connection with bigger organizational goals and to their work.
- Creation: To think about and solve problems associated with existing processes with innovative yet executable solutions.
- Control: A sense of ownership of a particular business process.
d. Agile Management
Agile is a flexible approach where teams work in short bursts to release a particular functionality of the product. They then test each release to match the customer’s expectations.
The end product may vary from the one which was envisioned at first but the functionality of the product matches the requirements of customers and satisfies their needs.
It is one of the fastest ways to release a product in an organized manner where several small functionalities are tested rather than the complete final product.
It is built on the product management idea of Takeuchi and Nonaka and incorporates the value and principles that were defined in the 2001 Agile manifesto.
e. Total Quality Management
Total Quality Management is the management approach of continuously detecting and removing errors to ensure long-term success. It helps in streamlining supply chain management and improving customer satisfaction, employee performance, and overall product quality.
Under this method, all the departments across the organization have to work towards creating value for the end customer. Whatever they do should create a positive impact on the customer. It holds all the stakeholders equally accountable for the final quality of the product or service.
Business Process Improvement Steps
After you select an ideal BPI methodology, it is time to start working towards improving the Business process. So, here are 7 basic steps that will help you kickstart your BPI journey.
i. Outline
The organization needs to identify where the problem is and which processes need improvement. You can also use a Digital Adoption Platform to identify processes that need improvement and immediate attention.
You can then allocate resources and strategies to the overall approach to address the process-related issues.
ii. Mapping
Once you have identified the processes that need improvement, you can document each step of the process using flowcharts, swim lanes, or workflow automation.
A flowchart is perfect if you have a small team but a swim lane is ideal for big teams with complex processes. Irrespective of the method you select, mapping the process needs attention to detail and with these traditional methods, there is a chance that you might miss a step or a workflow.
To counter this, you can use workflow automation software that will help you understand who is responsible for each step, giving you in-depth insight.
iii. Analysis
You can start analyzing the mapped processes and delve deep to understand the details that are causing the problem. It is important to use the right tool to find solutions to your problems. A Digital Adoption Platform (DAP) would be the perfect fit for this. Here are some information that a DAP can provide:
- Where employees or customers are getting stuck or facing issues
- Which step the problem arises
- Where employees or customers drop off
- What steps cause delays
- Which step has a higher impact on the bottom line
- Which segment of users is struggling more in comparison to others
Finding answers to these types of questions will help you find the pain points and the right solutions to overcome them.
iv. Redesign
Once the process analysis is done and you have identified the issues, you now have to redesign it.
First, go ahead and help the teams and departments that will be most affected by the change in the process, understand how the process works.
Explain what the process should accomplish, discuss the problems that you have identified in the analysis phase, and ask them for their opinion. This will help you understand other possible solutions for the issue and also reduce resistance to change.
Once you have selected the new process, set the right metrics to compare its impact with the old process. Perform different types of analysis like risk, impact, employee, and customer experience analysis to gauge the complete effect of the new process on your organization.
All this will help you get a comprehensive understanding of the impact that the new process may have on the product. It is important to document everything in a centralized hub to get input from all the stakeholders and identify issues beforehand if there are any.
v. Implement
Implementation is the most critical phase during the process improvement cycle. Don’t implement the new processes all at once because if something goes wrong, it could have a drastic impact on the organization.
First, test it within a focus group and check its efficacy for the short and long term. It will help you mitigate risks and overcome issues.
Use the right software, tools, and experts to implement the process. Get help from a consultant to stay on track and create realistic benchmarks.
Even if you have prepared all the stakeholders during the first three-phase there is still a high probability of internal resistance during implementation.
So, it is recommended to use change management models like Kotter-8-step-change-management-model to prevent this and motivate them to accept change.
vi. Automate
After the successful implementation of the new business process, the focus must shift to identifying repetitive tasks as it can consume valuable employee time which could otherwise be put to better use.
You can use tools like Digital Adoption Platforms to identify and automate repetitive tasks. A DAP like Apty that is powered by an AI engine, can help you identify tasks that most consume your employee’s time. Based on this insight, you can find processes that can be automated and successfully save time.
vii. Review and Refine
Improvement is a continuous process and even after having several checks in place, there can still be some aspects of the process that will need your attention. For this, you need to regularly review the process and refine it.
It can be achieved with the help of a tool like a Digital Adoption Platform(DAP) which can empower the organization by providing detailed process insights.
Conclusion
Business process improvement can benefit businesses from any industry, big or small. You need to constantly make improvements to your business operations in order to stay relevant and cater to your stakeholders and customers effectively.
Irrespective of how efficient your processes are, having a DAP in your organization’s toolkit will help you analyze, optimize and enhance your workflows and processes for better results.