COVID-19 has disrupted the global supply chain which has impacted the world economy. The healthcare and retail industry has been affected as providing medicines and daily essentials remotely to customers is impossible.
In 2020, some countries completely shut down because of COVID-19 and the supply chain as a result was severely impacted in an unprecedented manner. Once that problem was sorted, issues like the Swiss canal blockage and trade wars took place, which again stretched and strained the global supply chain.
A similar confluence of the supply chain 20 years ago would have crumbled the world economy but today supply chains have managed to survive even after many severe hiccups.
However, many companies and industries still need to amp up their game to be prepared for such scenarios. This can be achieved by adopting modern technologies and reengineering old business processes.
In this blog post, we will explore the latest trends, technologies, processes, and innovations that companies have adopted to counter the uncertainties of the past 2 years.
What is Digital Transformation in Supply Chain?
A Digital Transformation in the supply chain refers to the use of technologies and modern applications to improve the agility, capability, efficiency, productivity, and ROI of the company.
It helps companies deliver higher value to customers at an affordable price. Digital transformation in supply chain management is not just about technology adoption but also about a shift in how the business is being conducted.
How do you digitize a supply chain?
Supply chain digitization is the enablement of digital products and services to evolve traditional supply chains. Digital technologies in supply chains have enabled various industries to improve connectivity, efficiency, experience, and overall adoption of new processes.
The supply chain is extremely siloed but with digitization, the transparency and visibility are increasing across the board, helping supply chain managers to handle downstream and upstream efficiently.
You can digitize your supply chain by including technologies or platforms like data analytics, IIoT(Industrial Internet of Things), logistics platforms, Digital Adoption Platforms, and Control tower 2.0.
Digital Transformation Trends in Supply Chain Post Pandemic
1. Digital supply chain
The digital element has been present in the supply chain has been for many years but it took center stage in the last two years and helped several industries enhance their upstream and downstream to match the customers’ demands.
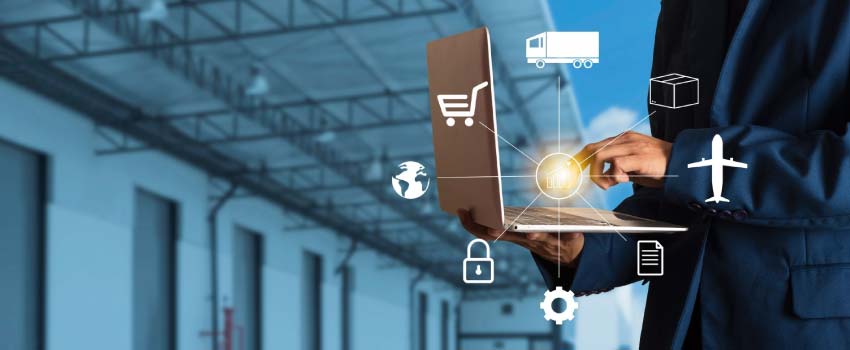
The main goal of the companies was to get visibility but with on-premise and outdated technologies, they were in a fix as handling demand spike, remote workers, and supply chain uncertainties was difficult.
To overcome this problem, companies started to invest in technologies like AI, ML, IIoT, Cloud, DAP, and Control Towers.
This not only helped them manage remote workforces and handle the supply chain disruption but also enabled them to get greater visibility on their entire supply chain.
Some successful companies were able to deploy what Gartner refers to as “multi-enterprise supply chain business networks” to gain greater visibility that goes beyond Tier 1 and Tier 2 suppliers and helps the company match the actual demand of the customers.
It has become one of the most important aspects of Digital Transformation in the supply chain as it helps companies increase efficiency, reduce risks, boost ROI and leverage new opportunities.
2. Smart control towers
Companies need greater visibility to predict demand and manage their inventory to satisfy the needs of the customers by supplying at the right place and at the right time.
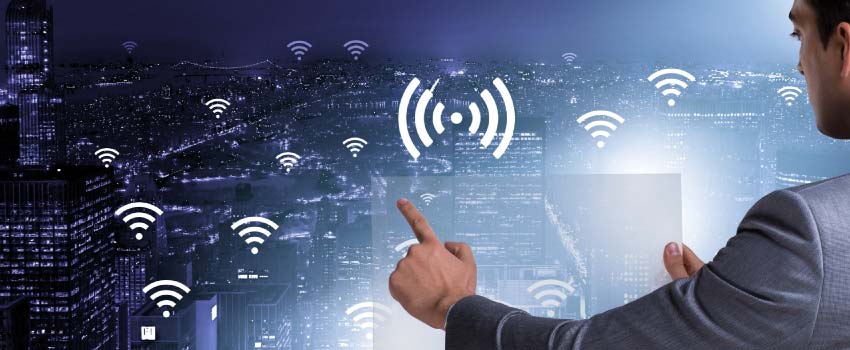
According to McKinsey, 39% of Industry leaders are leveraging Industry 4.0 and have implemented the nerve center approach which is also called a control-tower approach.
It helps them monitor and adjust the entire supply chain as it provides an understanding of their current inventory, resources, and their status.
Modern control towers are enabled with AI and ML to predict potential problems and provide you with relevant solutions that can be implemented instantly. This is also called the ‘anticipate, sense and respond’ capability which makes the supply chain of any company agile and flexible.
3. Robust information system
The drastic surge in demand for several products during the pandemic reinforced the importance of ‘information on time’.

If there is supply risk anywhere within the supply network, that information must be available for all. After the impact of the pandemic in 2020, companies have started to improve their communication and collaboration platforms.
Tools like real-time business network platforms empower the entire supply chain with current information. Some organizations also focus on using solutions like DAPs to communicate changes in price or raw material within the application that they use.
4. Go beyond ERP Barriers
Companies with a global presence have separate ERP instances which could lead to a surge in support tickets, massive buffer in inventory management, increase the load on IT, cause information lags and eventually confuse users while they use ERP systems.

All this can create a delay in the supply chain which can create a severe impact on your bottom line. The ideal solution would be to minimize the number of ERP instances but doing so can be challenging and in some cases impossible, due to complications in the business or geographical barriers.
Solutions like DAPs are helping companies guide employees and other stakeholders to learn complicated ERP processes in a matter of minutes.
The capabilities not only enable users to learn the process but also to execute their tasks by being compliant. It has helped organizations receive clean data which they use to make crucial business decisions.
5. Focus on Process Transformation
Firms have realized that over-reliance on a few suppliers might impact their inventory and overall supply chain efficiency. This is especially true when a disruption occurs within the industry because of macroeconomic events.

In any case, when an organization is presented with an opportunity to establish a new plant or reengineer the existing one, it is an opportunity to revamp the existing process for better results.
For example, a big industrial equipment company already has two facilities in Detroit and San Francisco and recently they get an opportunity to start a new plant in Palm Bay.
When they start designing the processes of the Palm Bay plant, they can add ideal processes or workflows of both San Francisco and Detroit and eliminate those which do not add value to the final product.
This will result in a streamlined and efficient process than the one they already use in their existing facilities.
When an organization tries to improve existing processes by using the latest technologies or applications, they can boost their product quality and profits.
They can also operate in different geographical regions reducing risks and enhancing their capabilities to operate in a collaborative environment around the globe.
Conclusion
Supply chains were running the marathon for decades but in the last 2 years, they have been participating in sprints and as a result, the industry has seen a positive shift.
There is still a long way to go and enterprises are worried about making their supply chain more resilient in the face of all the disruption.
So, companies with a global presence are looking to:
- create systems that are easy to navigate
- ensure the alternate way of supply as few countries were impacted during the disruption
- enable hyper and in-time collaboration of all the stakeholders
- gain greater transparency and insights
- invest in applications and platforms that can help employees instantly adopt new processes
Clearly, many industries are focusing in the right direction and with the right tools, technologies, and applications by their side they can improve their processes and streamline their operations to achieve maximum efficiency and satisfy their customer demands like never before.